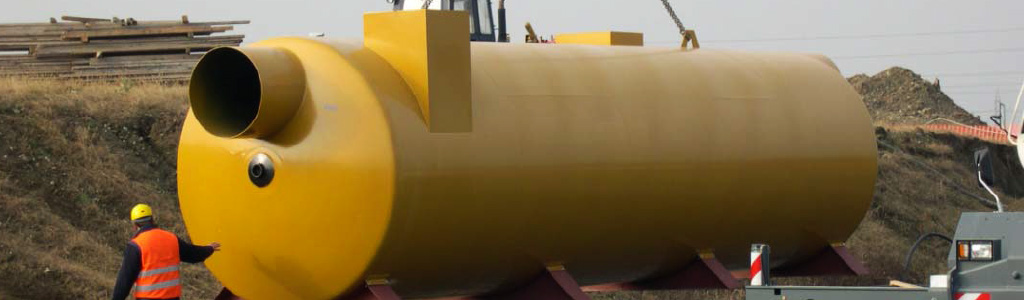
Lo sviluppo tecnico ed economico, a fianco dei grandi benefici che ha portato, ha messo in evidenza quanto sia sensibile l’ambiente e quanto sia elevato il rischio che questo subisca alterazioni da sostanze che vengono sempre più frequentemente e massicciamente impiegate.Tra queste sostanze gli idrocarburi hanno assunto un ruolo sempre più importante e, dato il loro elevato potere inquinante, richiedono una grande attenzione durante il loro utilizzo ed un sempre più attento controllo per evitarne la dispersione nell’ambiente.Non si può tuttavia evitare che le perdite di idrocarburi per sversamenti o gocciolamenti possano contaminare le acque come durante le operazioni di manutenzione delle apparecchiature meccaniche, il lavaggio degli automezzi e il dilavamento delle superfici stradali provocato dalle acque meteoriche.
La normativa italiana, a partire dal D.Lgs. 152/2006, indica dei limiti di concentrazione ammessi nelle diverse situazioni di scarico. In queste situazioni si rivela indispensabile l’impiego dei separatori di idrocarburi. La progettazione e la realizzazione di queste apparecchiature sono disciplinate dalle norme UNI EN 858.
Queste norme, che hanno sostituito le DIN 1999 di cui riprendono l’impostazione, indicano le caratteristiche costruttive, le modalità di prova e le procedure di scelta; indicano inoltre le modalità per eseguire i test di efficacia e suddividono i separatori in due classi:
- classe II: tenore residuo di idrocarburi < 100 mg/l
- classe I: tenore residuo di idrocarburi < 5 mg/l
Questi ultimi, per ottenere una migliore rimozione delle particelle più fini delle sostanze leggere, sono dotati di dispositivi denominati “a coalescenza”, che hanno lo scopo di aggregare le particelle e, aumentandone le dimensioni, facilitarne la separazione dall’acqua. Un buon sistema di separazione degli idrocarburi deve garantire facilità di manutenzione, rendimenti elevati e costanti nel tempo.
Il sistema risulta particolarmente efficace in quanto comporta un effettivo aumento della superficie attiva di flottazione (la risalita in superficie delle particelle di olio è tanto migliore quanto maggiore è il coefficiente di separazione, espresso di solito in m2/lxs, vale a dire quanto più elevata è la superficie attiva del separatore).
Inoltre, a differenza di altri sistemi quali ad esempio i filtri a coalescenza, non è soggetto ad intasamento e quindi oltre a non richiedere una sostituzione periodica garantisce la costanza dei rendimenti nel tempo. E’ importante sottolineare che questa costanza dei rendimenti nel tempo, non dipende tanto dall’efficienza dei controlli in fase di gestione quanto dal sistema stesso.
Questi dispositivi, inoltre, devono essere dotati di otturatore galleggiante per evitare la fuoriuscita di idrocarburi dall’apparecchiatura in caso di sversamenti occasionali o di eccessivo accumulo di queste sostanze per carenza di manutenzione.
E’ opportuno sottolineare che questi sistemi agiscono riducendo il contenuto di oli minerali leggeri ed idrocarburi non emulsionati e delle sostanze più leggere dell’acqua e sono preceduti da una fase di decantazione per la rimozione dei solidi decantabili. Sostanze presenti in emulsione, solidi in sospensione non decantabili e, in generale inquinanti in forma disciolta possono, quando richiesto dall’autorità competente, essere rimossi solo con trattamenti specifici.
Per la scelta del separatore è necessario individuarne la Taglia Nominale (TN), espressa in l/s.
Utilizzati nella maggior parte delle situazioni, sono composti dalle seguenti sezioni:
- sfangatura per la rimozione dei solidi decantabili; la sezione, che può essere diversamente dimensionata, è dotata di griglia in acciaio inox per impedire il passaggio di eventuali materiali galleggianti di grosse dimensioni alle fasi successive
- flottazione per la rimozione degli oli minerali leggeri e degli idrocarburi; la sezione è dotata di filtro a coalescenza lamellare a struttura incrociata in polipropilene smontabile atto ad aggregare le particelle di dimensioni minori per favorirne la risalita e presa a sifone con otturatore automatico quale sistema di sicurezza per impedire la fuoriuscita dallo scarico degli idrocarburi accumulatisi nel separatore
Nel caso di separatori adibiti al trattamento di acque di origine meteorica, è necessario tenere conto della possibilità di eventi meteorici di intensità superiore a quella adottata per il dimensionamento. Di conseguenza dovrà essere previsto a monte del separatore un idoneo pozzetto scolmatore in grado di evitare l’ingresso nel separatore di portate superiori alla massima ammissibile.
Le diverse tipologie impiantistiche sono le seguenti:
Serie Oil-I-Mp - Impianti realizzati in c.a.v.
Costituiti, in funzione della Taglia Nominale, da uno o due manufatti monoblocco prefabbricati in c.a.v. a conformazione parallelepipeda a sviluppo orizzontale. Sono possibili due alternative strutturali: vasche dimensionate per un carico distribuito di 1.800 kg/mq e vasche dimensionate per un carico distribuito di 5.500 kg/mq.
Serie Oil-I-Ca - Impianti realizzati in calcestruzzo alleggerito
Idonei solo per installazione interrata e possono soddisfare chi, oltre alla certezza di ottenere i risultati epurativi richiesti dalle norme, vuole un prodotto economicamente vantaggioso. Sono costituiti da un serbatoio parallelepipedo, composto da due semigusci rinforzati da nervature interne e legati tra di loro grazie a resine epossidiche e tiranti. I setti divisori interni sono realizzati in fibra di cemento.
Serie Oil-I-Pe - Impianti realizzati in polietilene
Idonei solo per installazione interrata e possono soddisfare chi, oltre alla certezza di ottenere i risultati epurativi richiesti dalle norme, ha bisogno di un prodotto leggero e di facile movimentazione. Sono costituiti da un serbatoio realizzato tramite stampaggio rotazionale utilizzando stampi specificatamente studiati per lo scopo. Il prodotto finale è caratterizzato da una elevata resistenza agli urti ed alla esposizione degli agenti atmosferici, è inoltre atossico.
Serie Oil-I-Av - Impianti realizzati in acciaio verniciato
Sono realizzati inlamiera di acciaio S 235 JRG. La protezione superficiale interna ed esterna viene eseguita con vernice bicomponente a base di resine epossidiche, dopo sabbiatura SA 2,5, conferisce ai manufatti una notevole resistenza nei confronti dell’acqua, dell’abrasione e di una larga gamma di prodotti chimici. Il pesoridotto fa si che buona parte dei modelli disponibili siano movimentabili con mezzi da cantiere.